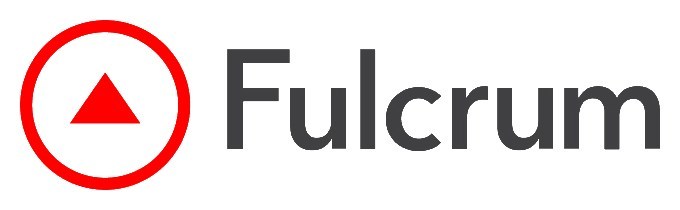
Fulcrum today announced new field inspection management functionality that improves efficiency, enables continuous improvement, and drives safer and higher-quality outcomes in the field, making it the first Field Inspection Management platform vendor to close the loop from inspection planning through issue resolution to auditing, reporting and analysis. Fulcrum customers can now obtain crucial insights at every level of an inspection workflow to inform workflow optimizations and plan new inspection processes.
“Fulcrum helps us improve processes and make our work environment safer by streamlining inspections, surfacing inspection-related insights, and managing follow-up actions,” said James Watts, Director of Health and Safety at Snavely Forest Products. “Once you close the loop from action to insight to further action, the possibilities are limitless.”
While a recent study from research firm paradoxes found that more than three-quarters of companies use digital devices to perform inspections, 70 percent also admit collecting some data using pen and paper, resulting in a significant lack of cohesion. For example:
- Since issue identification and remediation are often conducted by different teams, organizations get reduced visibility into their current tasking and safety, quality, and maintenance posture.
- Communication gaps lead to missed inspections, overlooked issues, and poor follow-up.
- Visibility into team performance is hampered by a lack of aggregated inspection, issue identification, and remediation data, which reduces the information available to help organizational leaders make decisions.
This lack of cohesion limits organizations’ ability to act on the inspection data they collect: They can only use it to execute a single desired task or achieve a specific desired result, such as triggering remediation. Closed-loop inspection management, by contrast, helps organizations plan inspections, detect issues, resolve them, and then drive actionable insights that feed back into the inspection management process. The result is optimized processes and better safety and quality outcomes.
Fulcrum’s new capabilities enhance organizations’ ability to close the loop from inspection actions to insights to new actions. Adding to Fulcrum’s best-in-class field inspection management platform, the closed loop functionality provides:
- Reduced risk through enhanced location intelligence for issues, which provides additional visibility and control of your quality and safety issue resolution processes.
- Elimination of inspection and remediation task communication gaps through improved notifications that provide reliable, consistent communication.
- Better inspection management and clarity in the field based on rapid, seamless deployment of the ideal inspection processes for each situation, ranging from simple checklists to advanced apps.
“Our customers tell us that they need better access to inspection data to improve their decision-making,” says Jim Grady, CEO of Fulcrum. “Fulcrum’s new capabilities ensure that their inspection data flows seamlessly into the remedial actions they take and future decision-making processes, so they get better performance now and continuous improvement as they move forward.”
For more information about how to close the loop with the Fulcrum Field Inspection Management platform, please visit our blog on fulcrumapp.com.
Fulcrum’s mission is to improve the way field teams work by automating inspection processes to ensure safer, higher quality, and compliant outcomes. We are committed to empowering field teams every day with our next-gen Field Inspection Management platform that improves team performance and safety, keeps projects on track, and eliminates regulatory compliance headaches. For more information visit fulcrumapp.com.
Fulcrum is proudly developed by Spatial Networks, Inc. Any trademark, service or other mark, other than Fulcrum which is used under license, belongs to the respective company owning such marks.